A Dynamic and Important Sector for Cables
Robotics, a key industry: experts discuss trends, opportunities and challenges
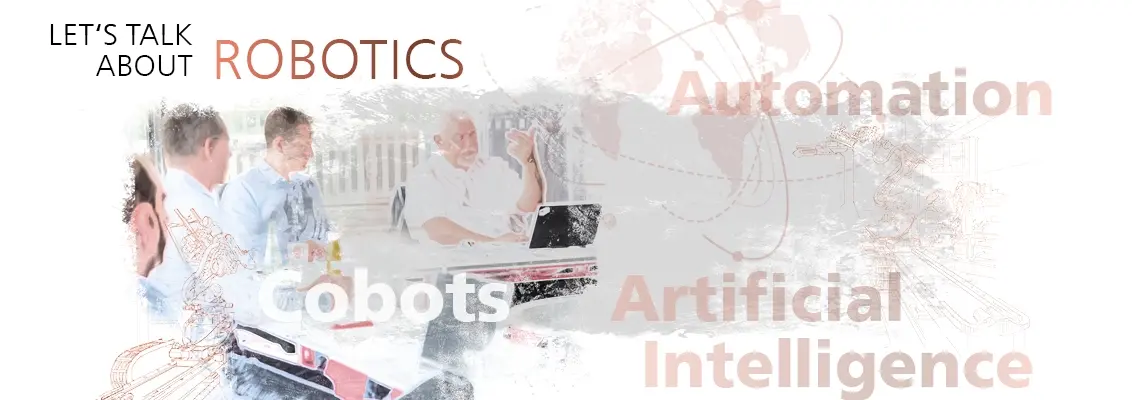
New applications in robotics are constantly emerging as the industry continues to develop new solutions to efficiently manage complex tasks. Consequently, robotics is a key industrial sector for HELUKABEL – cables and wires are, after all, indispensable in all types of robots. This is reason enough to closely look at the trends and challenges within robotics in a discussion between experts.
A particular image comes to mind when people talk about robots. But what actually is a robot and what is it not?
Prof. Christian Wurll: One definition specifies when a kinematic chain becomes a robot. It says that there should be at least three axes mechanically joined together. But there are lots of machines with only two axes – for example in the packaging industry – and these are also referred to as robots.
Ronald Benedek: But isn’t a machine tool then also a robot? These usually have more than three moving axes.
Dr.-Ing. Werner Kraus: The difference is that a robot can be used for a variety of applications, whereas a machine tool is built for a specific purpose, for example for milling. So, what a robot is and what it isn’t is open to interpretation. For instance, many manufacturers of driverless handling systems don’t consider themselves to be robot manufacturers but logistics providers. The question of autonomy also plays an important role in the definition.
Benedek: The typical image that comes to mind when talking about robots is the industrial robot in the factory – a mechanical arm that moves and turns.
What role do cables and wires play in robotics, and what requirements must they fulfil?
Holger Dietz: Six-axis robots are extreme environments for cables: they must withstand bending, torsion, tensile loads as well as other conditions. Robots also operate in extreme temperatures and come into contact with dust, dirt, moisture and chemicals. This really is a particularly challenging environment.
Janik Ebner: Cables and connectors are critical components in robotics where there is a risk of failure after millions of movement cycles. It goes without saying that our robots are designed so that the cables never kink. But it’s torsion in particular that can’t be avoided in many applications.
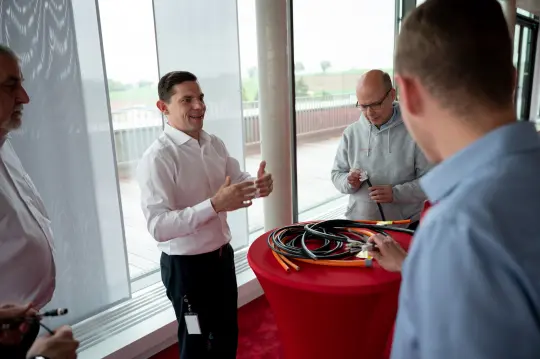
Benedek: It is this aspect, above all, that makes robotics such a fascinating area for us as a cable manufacturer. In order to enable movement along their longitudinal axis, our robotic cables are constructed very differently to other cables. This begins with stranding and goes beyond the conductor insulation and twisting to special foils and fleeces which are fitted into the cable to make them torsion resistant.
Vincenzo Rio: When it comes to robots used for welding, the issue of welding spark resistance also needs to be taken into account. We’ve been getting more and more inquiries lately about this, including ones from the automotive industry.
Dynamic loads are therefore the biggest challenge for components in robotic. How can a reliable performance be ensured and how can potential faults be detected early on?
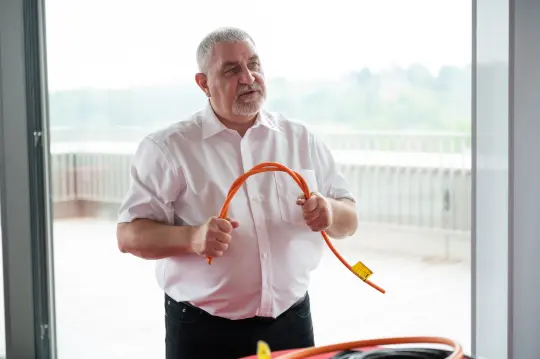
Horst Messerer: Of course, we spend a lot of time thinking about the service life of our cables - but the cable is only one part of the robot. There are also electronic components that can break, or bearings and motors that can wear. Even data cables grow old over time and become more susceptible to faults. In applications with real time data transmission, packet or bit errors will eventually affect the performance of the overall system. For example, it could affect the timing of a machine. But where the boundaries lie very much depends on each individual case. This is why condition monitoring of data cables is also a concern of ours.
Ebner: For predictive maintenance, diverse data, such as the distance travelled by the motors, is collected and transmitted from the robot. Based on empirical data, for example, it’s possible to very accurately predict when an axis needs to be serviced or a tool needs to be replaced.
Dietz: Robots in the automotive sector – for example on welding lines – have a service life of up to 16 years. The right cables can cope with that without any problems. In addition, the topic of retrofitting robots is currently on the rise. Because the delivery times are sometimes very long for new models, there’s a lot to be said for retrofitting and repairing old robots. It might also be a good idea to replace the cables at the same time.
Wurll: When a robot stops working properly, it’s most likely due to a broken peripheral component such as a gripper or the welding technology. Their repair is the responsibility of the system integrator who fitted the robot with the components. Peripherals account for the bulk of the costs of most robotic systems. Therefore, this is where the focus should be when it comes to planning predictive maintenance.
The spatial separation between humans and robots is diminishing in many jobs – keyword cobots. In your opinion, what challenges are associated with this?
Kraus: One of the most important points is to avoid accidents as much as possible. After all, the risk of being injured by a cobot without a safety fence around it is significantly higher than by an industrial robot in a completely enclosed space. People working with robots need to be appropriately trained, for instance by passing a sort of “robot driving test”. The fact that robots are also capable of executing unexpected movements at any time is often overlooked - This can quickly cause collisions. It’s for this reason that the travel speed of cobots is significantly slower.
Dietz: There have been attempts to monitor the behaviour of cobots using cameras in order to evaluate collisions and prevent them in future. Depending on the application, data protection rights need to be observed here as workers might feel that they’re under surveillance by such systems.
Ebner: It’s also worth mentioning that even though it’s possible to work collaboratively without spatial separation between the human and robot, there are plenty of operators who don’t want to do this. As a consequence, in practice, cobots are often not used as cobots, i.e., as collaborative robots, in the true sense of the word, but as compact variants of the more traditional industrial robot.
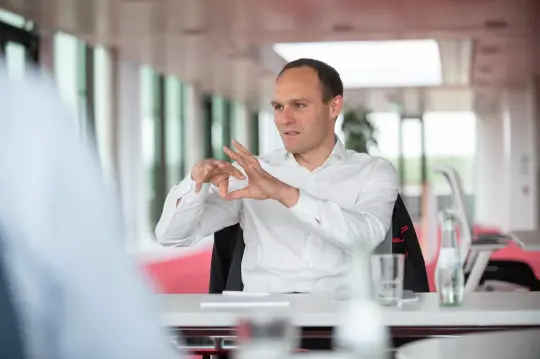
Cobots and a new generation of easy-to-operate industrial robots are facilitating the move to robotics for many operators. But when is the right time to invest in robotics and what benefits can be expected?
Ebner: This very much depends on the application in question. In general, cobots and a new generation of compact and easy-to-operate industrial robots, like our HORST, are aimed at small and medium-sized companies, of whom, up to now, have only a small percentage of robots in use at all. It’s not a matter of high-end applications but rather of gaining initial experience with the technology and discovering how to move into this area in a straightforward and economically viable manner. It often starts off with the idea of procuring a robot, and the concrete application crystallises only later on – it’s de facto the opposite of how it is with the traditional robots we are familiar with in the automotive industry, for example. Cobots and the new generation of industrial robots are also far more flexible and are not designed to repeat the same task over and over again for six or ten years. They offer a completely different level of accessibility, both in terms of price and in terms of set-up and operation. This is why we’re convinced that there is still great potential here.
In the course of digitalisation, the question is asked time and again about whether automation and robotics will destroy jobs or create new ones instead. In which key technologies will jobs performed by humans be taken over by robots? Where do you see opportunities and possibilities for new jobs to be created through robotics and automation?
Dietz: I don’t see robotics as a threat to human jobs, but rather as an enhancement. Here in Germany there’s a shortage of skilled labour; it’s getting more and more difficult to find qualified workers for many jobs. Robots can take over physically demanding or monotone jobs that humans don’t like doing – and that seven days a week, 24 hours a day, without any breaks and to a high degree of accuracy. I think it’s unlikely that jobs will disappear in these sectors because even today we don’t have sufficient numbers of skilled workers. It might be different in low wage countries where there’s a greater availability of labour. On the other hand, new jobs are being generated for people to programme and operate robots. Providing adequate training for staff to do these jobs though is certainly a big problem for companies. This is something we’ll have to tackle in the coming years.
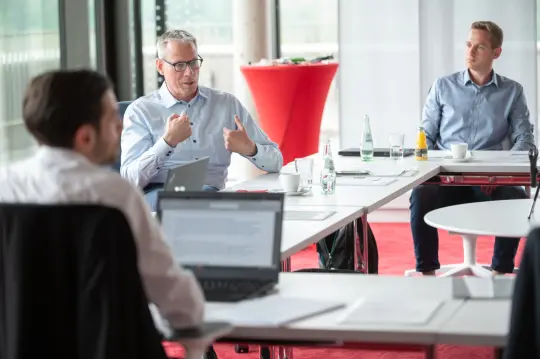
Whether in medicine and care, in gastronomy, private households or for children’s toys: the possible applications of robots seem almost unlimited, even outside of industry. Will we be surrounded by robots in all areas of life in 10, 20 or 50 years’ time?
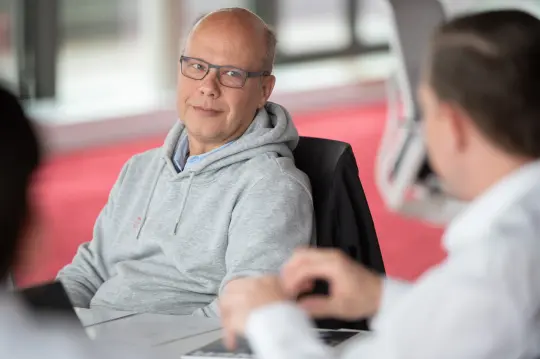
Benedek: I see a trend developing towards service robots. Robots will be deployed more and more in households, nursing homes and hospitals. For example, they’ll help people to lift heavy objects or do other things that they can’t do any more for health reasons. Robots already exist that autonomously go into hospital rooms, for instance, and disinfect them using UV light. I’m guessing there’ll be one or the other sensible or nonsensical idea for robots aimed at helping private individuals rather than industry.
Dietz: I see a lot of potential in the medical sector as well. Assisting robots are already being developed to perform endoscopic operations, for example. Such operations usually involve up to four doctors standing close to each other around the patient. By contrast, the robot has up to four arms and is controlled via a console, monitor and camera – this allows for a much better overview. Physiotherapeutic treatments or adjustable operating theatre tables are other major up-and-coming areas of application. Moreover, the use of robots is obviously preferable when it comes to working in areas that pose a danger to health or life, such as bomb detonation or nuclear reactors.
Wurll: We’re currently spending a lot of time on construction sites where we’re working with a construction firm to develop a robot to build limestone walls. Robotics is also an interesting area for farming. We’re in contact with a number of grab manufacturers who are contemplating automated strawberry or apple pickers. Outdoor suitability plays an important role here of course. The technology must work in all types of weather. Companies such as Google are investing huge amounts of money in so-called Everyday Robots. These are mobile platforms with arms that can straighten up chairs and clean tables in restaurants and cafés, for example. Whether they’ll really take off in the sector is hard to say at the moment but they’re definitely a new trending topic in gastronomy.
Kraus: I think the advances made by robotics in manual activities are significantly greater than those made in language-based interactions. There’s an interesting parallel here to the evolution of human language skills, which developed noticeably later than our dexterous skills. Similarly, in my opinion, it’s going to be hard for us to model and master this in the form of artificial intelligence. That’s why, it’s my belief that the next robot revolution is going to be mobile platforms for use in logistics, for instance.
Wurll: There are already innovative approaches for loading lorries and swap bodies. An American supplier recently demonstrated a mobile platform with a custom-developed arm that had been optimised for a swap body. The robot is capable of moving into the load carrier and localising and loading boxes using a telescopic conveyor. It doesn’t necessarily do this more quickly than a human being, but it doesn’t need any breaks. This means that there are already potential productivity benefits.
Kraus: Another application that’s currently emerging at a very rapid pace is the welding robot. The shortage of skilled welders is particularly acute, and it doesn’t matter if the robot moves slowly – welding has always been a job that takes time. One of the topics we’re currently working on at the IPA is therefore the intelligent recognition of the beginning and end of a weld and making automatic adjustments based on weld tolerances. We reckon there’s a lot of potential for robotics in welding.
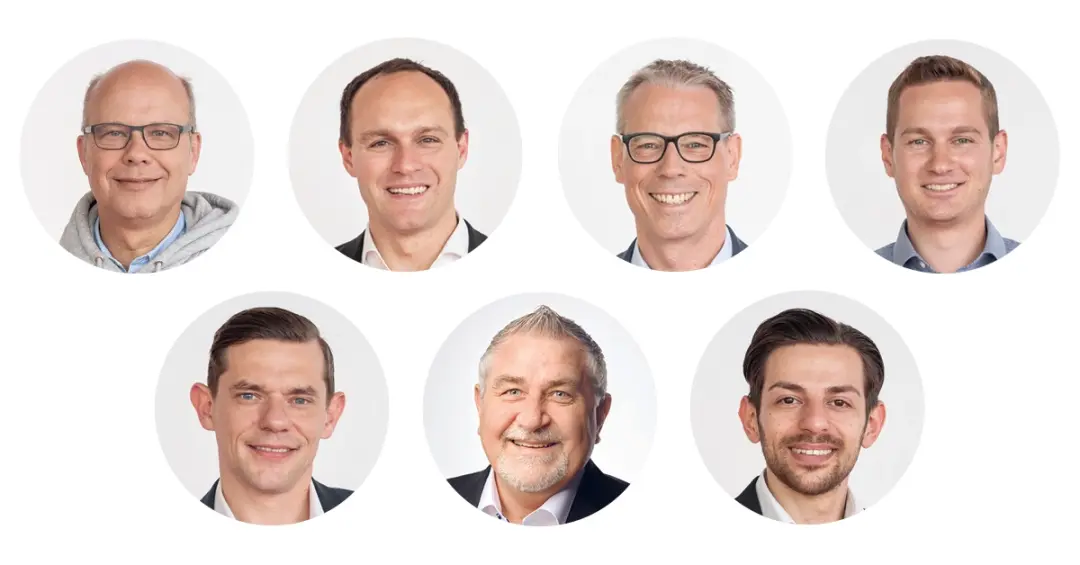
About the People
- Prof. Dr.-Ing. Christian Wurll is Professor of Electrical Engineering and Automation in the Faculty of Management Science and Engineering at Karlsruhe University of Applied Sciences. His specialist area is robotics and automation engineering. He is also spokesman of the Institute of Applied Research. He previously worked at the robot manufacturer Kuka for 16 years.
- Dr.-Ing. Werner Kraus is Head of Robot and Assistive Systems at the Fraunhofer Institute for Manufacturing Engineering and Automation IPA in Stuttgart. Among other things, the institute is building a “Robotics Valley” in Baden Württemberg with the aim of bringing together various players in the field of robotics.
- Janik Ebner is Project Manager at fruitcore robotics GmbH. In 2018, the company based in Constance launched the HORST industrial robot onto the market, which particularly enabled small and medium-sized companies to have a simple and affordable entry into robotics.
- Holger Dietz is Business Unit Manager at Robotec Systems GmbH, a subsidiary of HELUKABEL. The Duisburg company specialises in hose packs and dress packs for media technology in industrial robotics. Dietz’s previous job experience includes working for various mechanical and plant engineering companies, including Kawasaki Robotics.
- Ronald Benedek has been with HELUKABEL since 2008 and, in his role as Automation & Drives Team Leader, is in charge of topics relating to drive technology and robotics.
- Vincenzo Rio has been reinforcing the team around Ronald Benedek since 2020 as Expert for Robotic Cables. His tasks include managing industry-specific product portfolios and supporting HELUKABEL’s international subsidiaries.
- Horst Messerer is Data, Network and Bus Technology Product Manager at HELUKABEL. Before joining the company in 2014, he spent 28 years in the cable industry. He is also active in various bus and Ethernet associations and is very well-acquainted with current standards.
You can also find this and many other exciting articles in the current issue #12 of our customer magazine POWER. Read it now!